Inconel625/UNS NO6625/NS 336
Inconel 625 alloy is a solid solution strengthened nickel-based deformed high-temperature alloy with molybdenum and niobium as the main strengthening elements. It has excellent corrosion resistance and oxidation resistance, and has good tensile properties and fatigue properties from low temperature to 980°C. Resistant to stress corrosion in salt spray atmosphere.
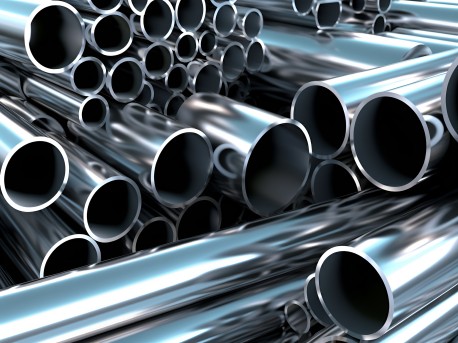
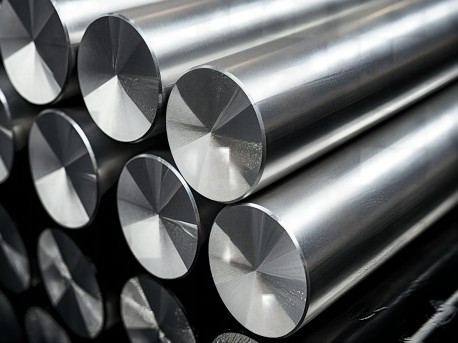
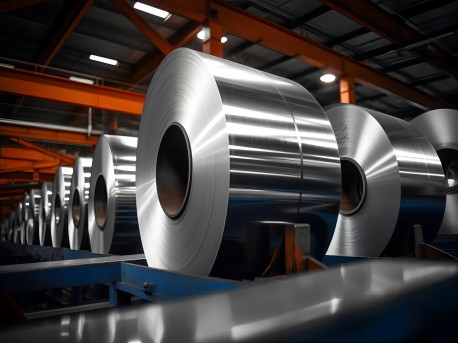
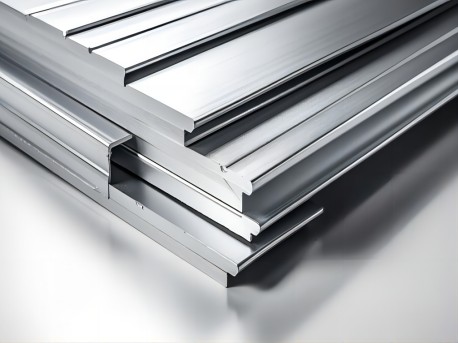
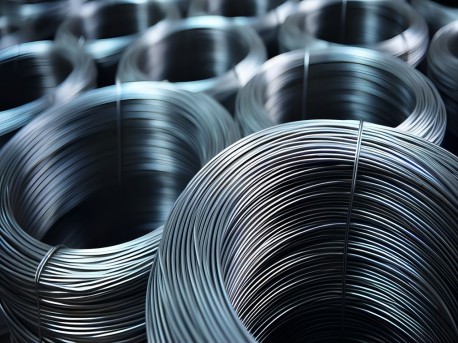
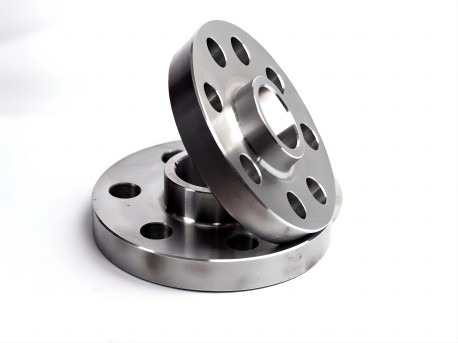
Inconel625/UNS NO6625/NS 336
Product Description:
Inconel 625 alloy is a solid solution strengthened nickel-based deformed high-temperature alloy with molybdenum and niobium as the main strengthening elements. It has excellent corrosion resistance and oxidation resistance, and has good tensile properties and fatigue properties from low temperature to 980°C. Resistant to stress corrosion in salt spray atmosphere.
Therefore, it can be widely used in manufacturing aerospace engine parts, aerospace structural components and chemical equipment. This alloy is used to manufacture parts such as engine casings, guide vanes, mounting edges and barrels, and fuel main pipes. It has passed practical application assessments and has a maximum operating temperature of 950°C. The alloy has a certain aging effect after long-term use at 550 to 700°C. The hardening phenomenon leads to some decrease in the plasticity of the alloy.
Physical properties:
Density: 8.4g/cm³
Melting point: 1290-1350℃
Extreme chemical composition: %
Nickel: balance
Chromium: 20-23
Iron: 5max
Molybdenum: 8-10
Niobium: 3.15-4.15
Carbon: 0.1max
Manganese: 0. 5max
Silicon: 0.5max
Sulfur: 0.015max
Phosphorus: 0.015max
Aluminum: 0.4max
Titanium: 0.4max
Boron: 0.006max
Characteristic:
1. It has excellent corrosion resistance against various corrosive media in oxidizing and reducing environments.
2. Excellent resistance to pitting corrosion and crevice corrosion, and will not produce stress corrosion cracking caused by chloride
3. Excellent resistance to inorganic acid corrosion, such as nitric acid, phosphoric acid, sulfuric acid, hydrochloric acid and mixed acids of sulfuric acid and hydrochloric acid, etc.
4. Excellent resistance to corrosion by various inorganic acid mixed solutions
5. When the temperature reaches 40°C, it can show good corrosion resistance in hydrochloric acid solutions of various concentrations.
6. Good malleability and weldability, no post-weld cracking sensitivity
7. Manufacturing certification of pressure vessels with wall temperature between -196~450℃
8. Certified by the NACE standard of the American Society of Corrosion Engineers (MR-01-75) to meet the highest standard level VII for use in sour gas environments.
Application areas:
1. Components of organic chemical processes containing chlorides, especially where acidic chloride catalysts are used
2. Digesters and bleaching tanks for manufacturing pulp and paper industry
3. Absorption tower, reheater, flue gas inlet baffle, fan (humidity), agitator, guide plate and flue in the flue gas desulfurization system
4. for manufacturing equipment and components used in sour gas environments
5. Acetic acid and acetic anhydride reaction generator
6. Sulfuric acid condenser
Forms: Strips, plank stuff, round bars, flat bars, forged stocks, hexagons and wires