Incoloy800
Alloy 800 is an iron-nickel-chromium alloy with moderate strength and good resistance to oxidation and carburization at elevated temperatures. It is beneficial for high-temperature equipment in the petrochemical industry because the alloy doesn't form the embrittling sigma phase after long time exposure at 1200°F (649°C). Excellent resistance to chloride stress-corrosion cracking is another important feature of alloy 800.
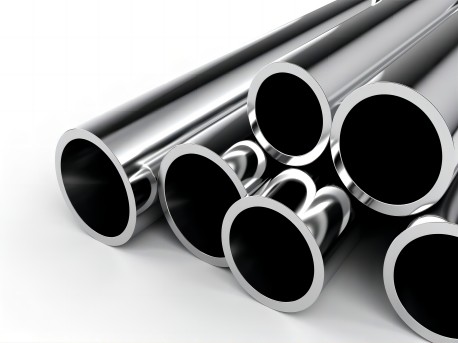
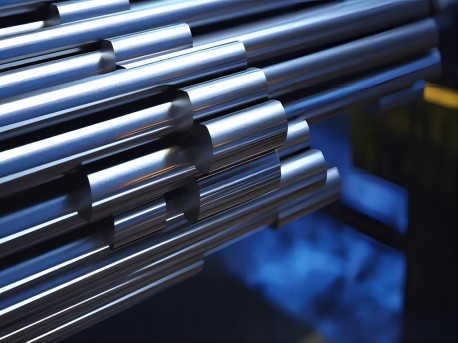
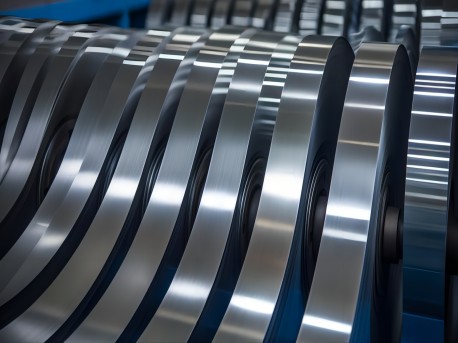
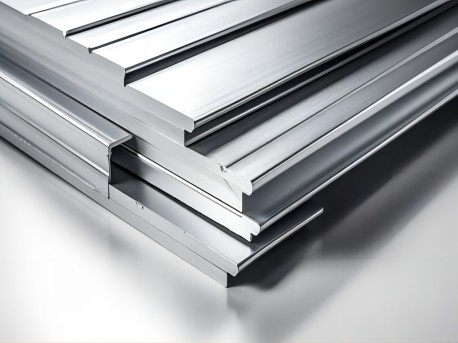
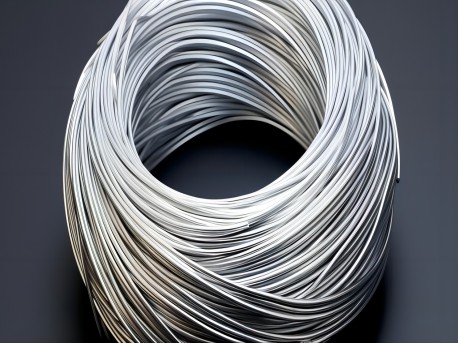
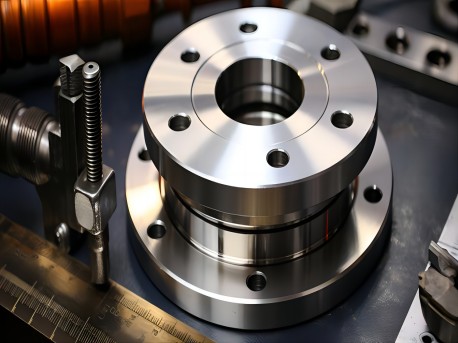
Incoloy800/800H/800HT(UNS NO8800/UNS NO8810/UNS NO8811)
Product Description
Alloy 800 is an iron-nickel-chromium alloy with moderate strength and good resistance to oxidation and carburization at elevated temperatures. It is beneficial for high-temperature equipment in the petrochemical industry because the alloy doesn't form the embrittling sigma phase after long time exposure at 1200°F (649°C). Excellent resistance to chloride stress-corrosion cracking is another important feature of alloy 800.
Alloy 800H is solution heat treated (2100°F/1150°C), a controlled-carbon version of alloy 800 with improved elevated temperature properties. It has improved creep and stress-rupture characteristics in the 1100°F (593°C) to 1800°F (982°C) temperature range.
UNS N08810 / UNS N08811
Incoloy 8Incoloy 800 H is an iron-nickel-chromium alloy having the same basic composition as Incoloy 800, with significantly higher creep rupture strength. The higher strength results from close control of carbon, aluminum, and titanium contents in conjunction with a high-temperature anneal. The 800H modification was to control carbon (0.05 to 0.10%) and grain size (>ASTM 5) to optimize stress rupture properties. Incoloy 800 H has further modified the combined titanium and aluminum levels (0.85 to 1.2%) to ensure optimum high-temperature properties. The alloy is dual-certified and combines the properties of both forms.
The chemical balance allows the alloy to exhibit excellent resistance to carburization, oxidation, and nitriding atmospheres. 800HT will not become embrittled even after long usage periods in the 1200-1600 deg F range where many stainless steels become brittle. Excellent cold-forming characteristics typically associated with the nickel-chromium alloys are exhibited with 800HT. When cold formed extensively the grain size produces a visibly undulated surface called "orange peel". 800HT can be welded by the common techniques used on stainless steel.
Typical applications for the alloy include ethylene pyrolysis, hydrocarbon cracking, and cracking furnaces for vinyl chloride, diphenol, and acetic acid.
Physical properties:
Density: 8.0g/cm³
Melting point: 1350-1400℃
Extreme chemical composition:
% | Ni | Cr | Fe | C | Mn | Si | Cu | S | AL | Ti | |
800 | min | 30 | 19 | 0.15 | 0.15 | ||||||
max | 35 | 23 | balance | 0.10 | 1.5 | 1 | 0.75 | 0.015 | 0.60 | 0.60 | |
800H | min | 30 | 19 | 0.05 | 0.15 | 0.15 | |||||
max | 35 | 23 | balance | 0.10 | 1.5 | 1 | 0.75 | 0.015 | 0.60 | 0.60 | |
min | 30 | 19 | 0.06 | 0.15 | 0.15 | ||||||
max | 35 | 23 | balance | 0.10 | 1.5 | 1 | 0.75 | 0.015 | 0.60 | 0.60 | |
AL+Ti:0.85-1.20 |
The minimum value of the mechanical properties of the alloy at room temperature:
Alloys | Typical mechanical properties | tensile strength Rm N/m㎡ | Yield Strength RP0.2 N/ m㎡ | Elongation A5% |
800 | 500 | 210 | 35 | |
800H/800HT | 450 | 180 | 35 |
Property:
INCOLOY alloys 800H and 800HT have significantly higher creep and rupture strength than INCOLOY alloy 800.
Good processability
Applications:
In the hydrocarbon processing industry, these alloys are used in steam/hydrocarbon reforming for catalyst tubing, convection tubing, pigtails, outlet manifolds, and quenching system piping; in ethylene production for both convection and cracking tubes, and pigtails; in oxy-alcohol production for tubing in hydrogenation heaters; in hydrodealkylation units for heater tubing; and in the production of vinyl chloride monomer for cracking tubes, return bends and inlet and outlet flanges. Industrial heating is another area of wide usage for both INCOLOY alloys 800H and 800HT. In various types of heat-treating furnaces, these alloys are used for radiant tubes, muffles, retorts, and assorted furnace fixtures. Alloys 800H and 800HT are also used in power generation for steam super-heating tubing and higher temperature heat ex-changers in gas-cooled nuclear reactors.
Form:
Pipes, tubes, sheets, strips, plates, round bars, flat bars, forgings, hexagons and wires.